Welcome to another installment in our “Building Barreto Tough” journey where we give our customers a behind the scenes look at our manufacturing process. If you are just joining us, we recommend starting here: Building Barreto Tough: CNC Mills and Lathes.
Today we will take a look into our welding and robotics department, where technology and craftsmanship combine to cover all aspects of our welded parts.
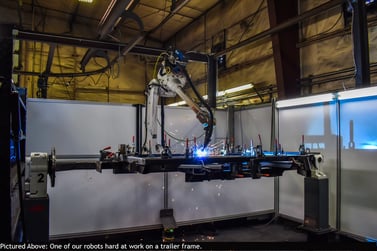
Robotics has been a staple in the manufacturing industry for many years. In fact, here at Barreto Manufacturing, we have been using robotics in our welding department since the mid-90’s. Our original robot welder was in operation until just a few years ago. We now employ the use of four robots in our welding department. Welding robots offer speed and consistency on parts with longer welds and they are capable of welding up to 25 in/min. They are also able to produce our high volume parts with greater efficiency and speed. With robotics, certain parts can now be welded in a matter of minutes, a significant improvement when compared to the hours it can take when done by hand.
Our robots are equipped with the ability to adjust and recalibrate themselves and are even self cleaning. Achieving results with this advanced technology wouldn’t be possible without our programmers, operators, and welders. Robotics allows our employees to focus on more intricate parts, where their craft is better utilized and recognized. It has also offered a unique experience for our employees, giving them the ability to learn and advance. Providing the opportunity for us to offer more entry level positions and student apprenticeships for those interested in learning the trade.
As demand for Barreto equipment grows, so does our parts production. Welding robots have allowed us to remove some of the strain from our welders themselves. With some of our larger parts now able to be welded robotically, we can reduce the burden of lifting and moving these pieces numerous times throughout the day, allowing our welders to focus on smaller parts more suitable for continuous handling.
Keeping our manufacturing in-house allows us to have control over quality and production in order for us to consistently provide the tough, durable products our customers know and love.